Machines
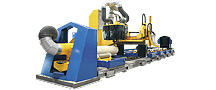
CPCut
CPCut is a pipe and profile cutting line designed for processing of a great range of pipe diameters and lengths. The machine´s modular design and variable execution enables a wide range of pipe based applications including trimming, cutting of various openings for multiple pipe and profile intersections or connections, welding seam preparation as well as pipe marking. The application field is in tank, pipeline and power plant constructions.
Technical parameters

Together with plasma rotator and advanced software modules
and libraries from MicroStep it offers the full range of
pipe based applications.

pipes and profiles. Together with plasma rotator
and advanced software modules and libraries from
MicroStep it offers the full range of pipe based
applications.

on a single Z lifter. Gm-type is dedicated for
cutting of stripes with oxyfuel torches.

automatically compensates by advanced motion
control any mechanical inaccuracy of the bevel
head which can occur e.g. by accidental collision.

bevel cutting at any point of the dome as well
as dome trimming. The variable bevel cutting
feature provides a constant welding volume
along the contour for robot welding.

system, which was designed for multi-purpose application in
industrial environment for marking of spongy and non-spongy
surfaces with variable height of letters from 3 to 124 mm.
The system marks various products by logos, bar codes,
information on minimal duration, charge numbers and commission
numbers, readers and weight values, continuous numbering and
production data (date, time, shift) etc. Marking can be lateral,
from above and from below through head.

marking of several types of materials –sheets,
tubes, profiles - with differently machined
surfaces.The material can range from plastics
to hardened steel.

or mounted on a separate toolstation. It is used for:
a) scanning of the shape of template for conversion into DXF
b) scanning of holes on plate for positioning

functions of a standard touchscreen integrated
in the MMI console. It is very helpful especially
in case of longer machines because the operator
can set all parameters (e.g. for automatic gas
console for oxyfuel) directly on the gantry.